A Pick to Light system streamlines the product selection process in warehouses. Using indicator lights, it shows staff the exact location of the item, optimizing order preparation time and minimizing errors.
Benefits
This system maximizes product storage in a limited space.
It greatly reduces picking time and the likelihood of picking errors, significantly increasing efficiency in order preparation, directly impacting key aspects such as:
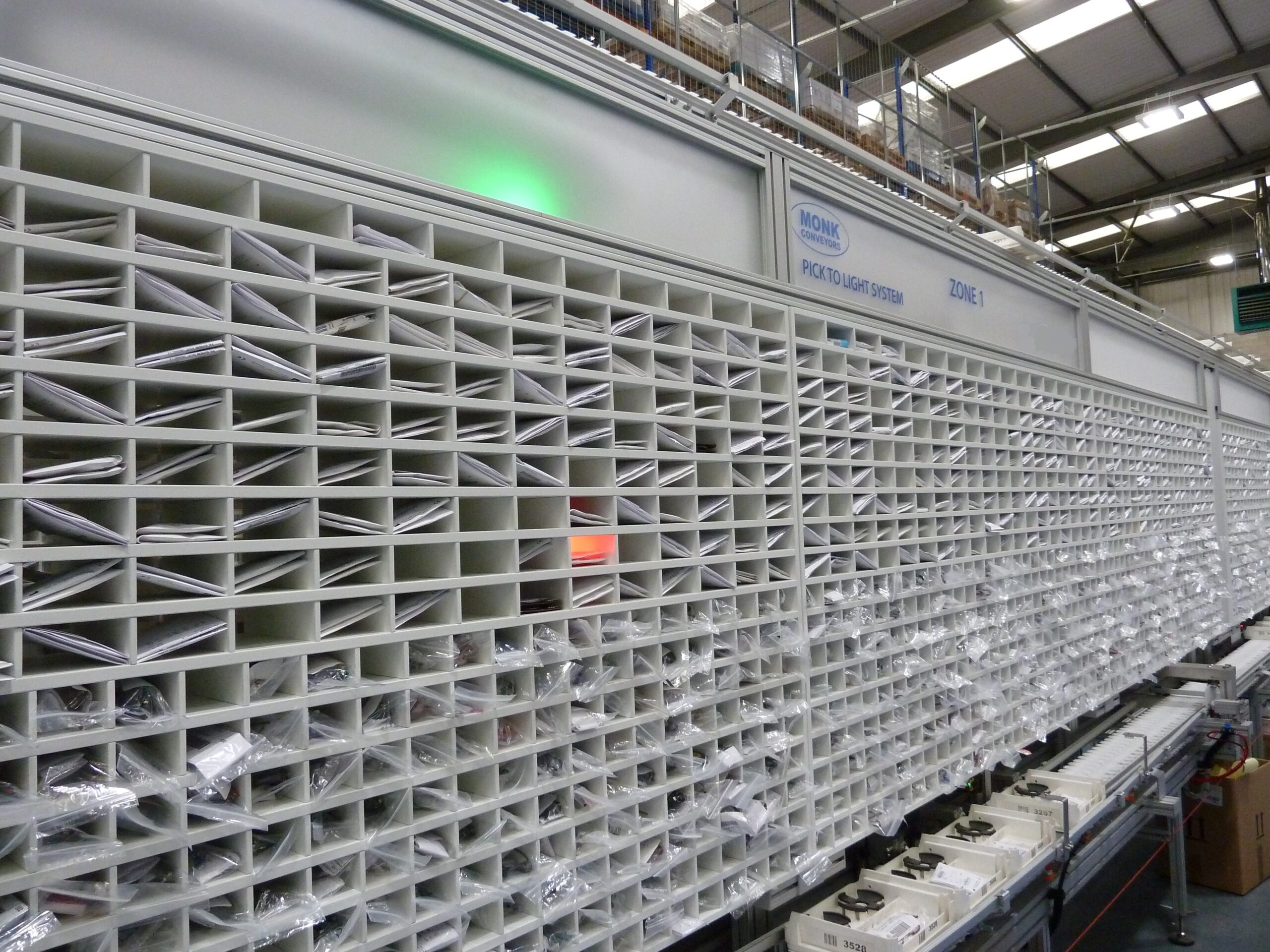
Picking Process with Pick to Light Technology and Barcode
The typical process uses our portable barcode system that scans the barcode or QR code label on both the product and the pick locations. When scanning a pick sheet or order, the product locations light up, guiding staff through the picking and verification process. The system can be customized to meet the needs of each warehouse, marking a task as completed and ready for shipment, or redirecting it to other areas of the facility.
Flexibility in Warehouse Configuration
Because each factory or warehouse operates with slightly different methods, our system is capable of adapting to your specific process. The pick locations can be set up as follows:
a) All with the same part number in one location,
b) All locations of a job/kit in one location.
This means that all parts in a location are exactly the same, and staff can pick one or more from the location when the light is on.
This means that the parts in a location must form a particular job/kit and therefore may not all be the same. It could be that 5 different parts from various suppliers are required to complete a job/kit. As parts are delivered throughout the day, they would be placed in the location. The light turns on when the kit is complete, making it easier to pick.
Efficient Storage Functions
The Pick to Light system not only facilitates picking, but also storage. By scanning the product’s barcode, the location where it should be stored lights up, ensuring fast and accurate placement, whether by part number or to complete a kit.
Zone Design for Greater Efficiency
The picking area is divided into zones, reducing movement and making it easier to locate products. This allows employees to work in different zones in an organized manner, increasing efficiency. A typical zone would be 5 to 8 meters long.
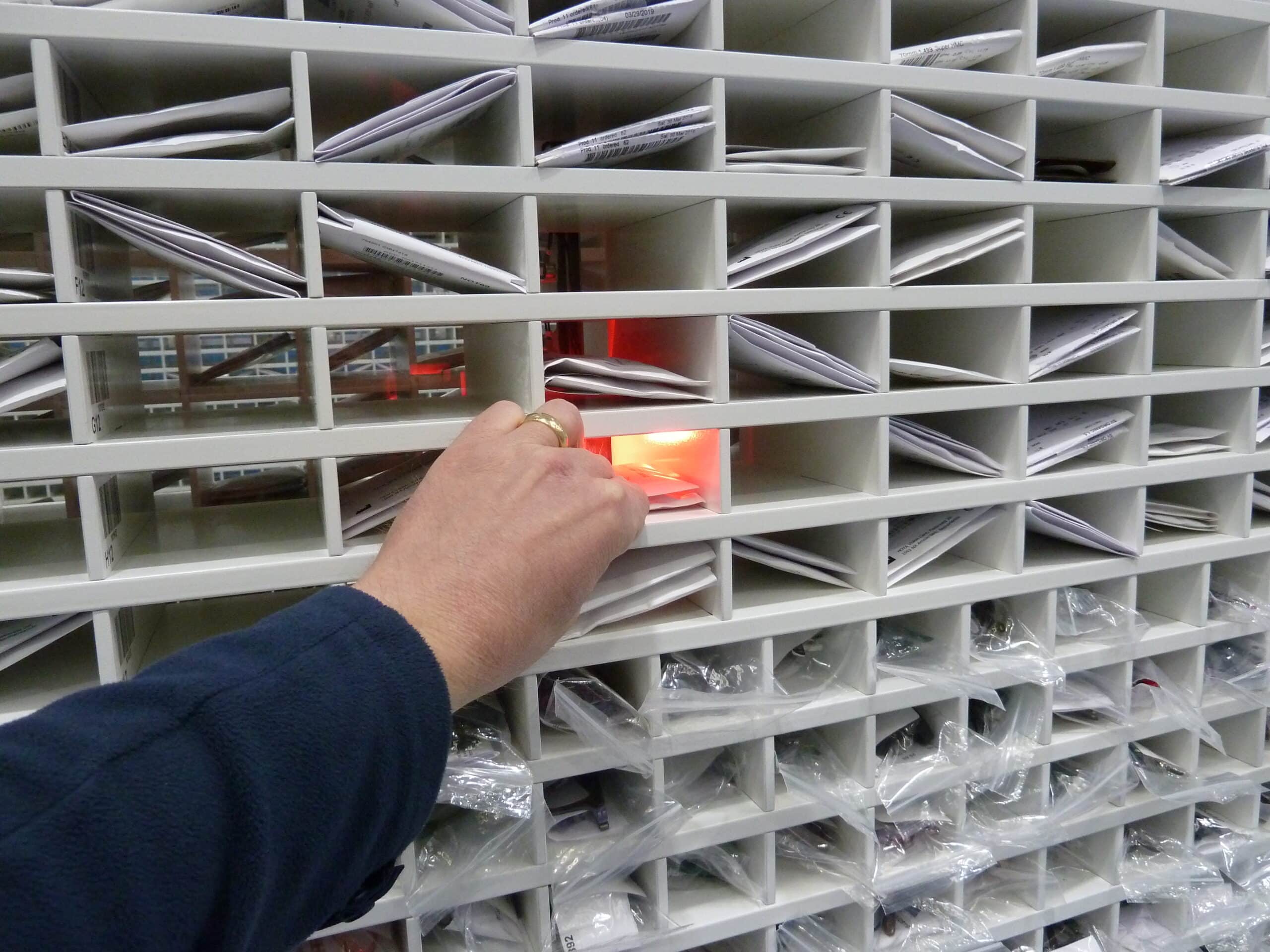
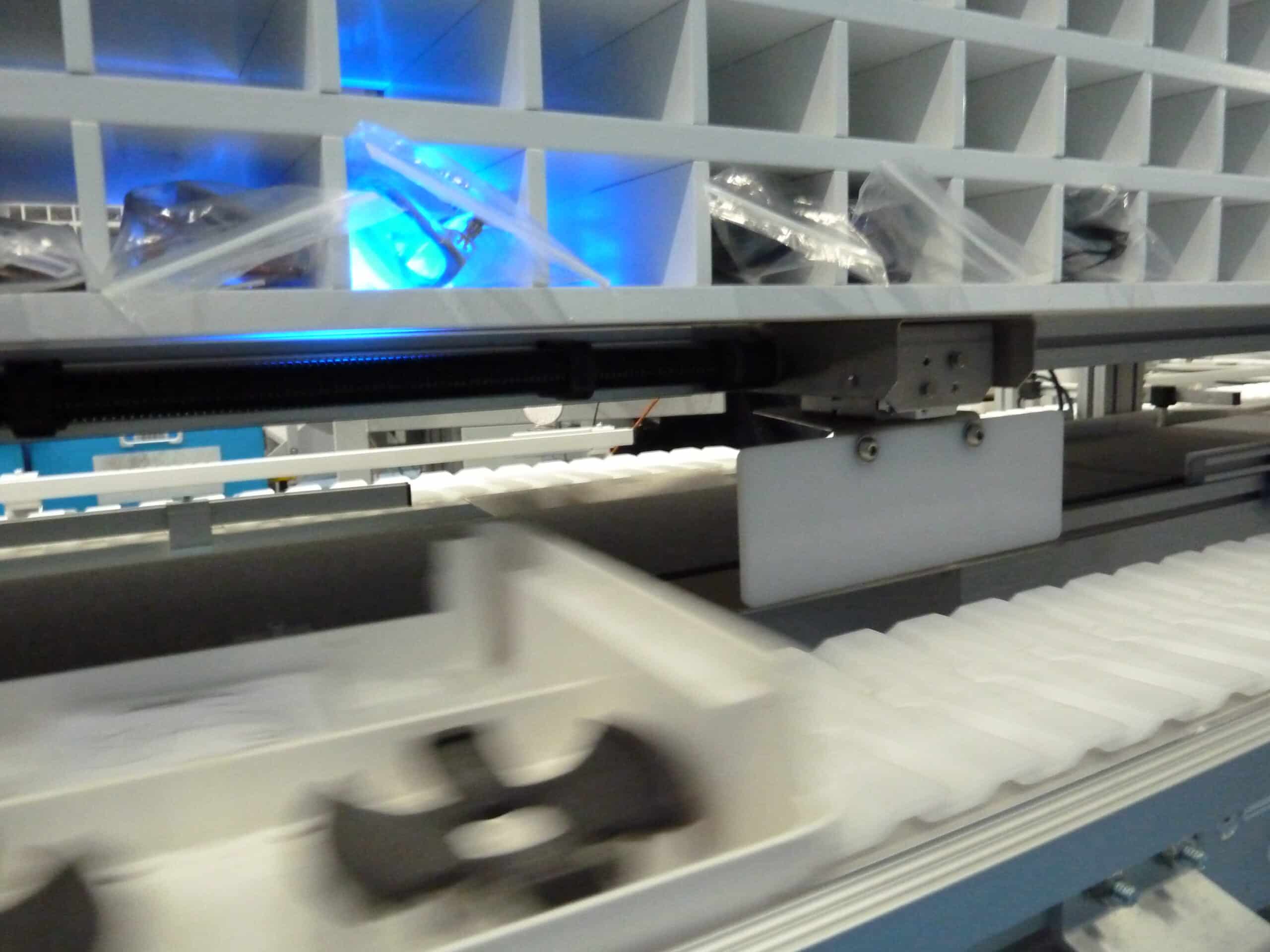
Adaptability for Picking and Storage
Depending on the operation within the facility, the same equipment can perform both picking and storage tasks, making it easier to work in warehouses with flexible hours and deliveries spread throughout the day. Our system allows for switching between picking and storage in seconds, maximizing efficiency and reducing the need for additional staff.
A typical scenario is when deliveries arrive in the morning and goods are shipped in the afternoon/evening. Staff can easily switch between Pick and Put Away throughout the day. Due to the system’s efficiency, a small number of employees can operate a large picking area.
Automation with Conveyor Systems
Conveyors are often used to transport individual products, trays, containers, or cardboard boxes to the picking face and directly to the correct pick zone, allowing staff to work focused in one area. This means that staff can work within a zone where the product is automatically brought to them, and the completed work is automatically removed once the picking is finished. This optimizes workflow and reduces order preparation time.
Specific Solutions: Pocket and Drawer Pick to Light
Pocket – Pick to Light System: Suitable for small products in the optical, pharmaceutical, medical kits, tablets, medications, and dispensaries industries. It allows for storing a large quantity of product in a small area for easy and organized preparation. The cavities are made to a size that works well with the product and the process. The cavity locations can be used to store the product by part number or job/kit.
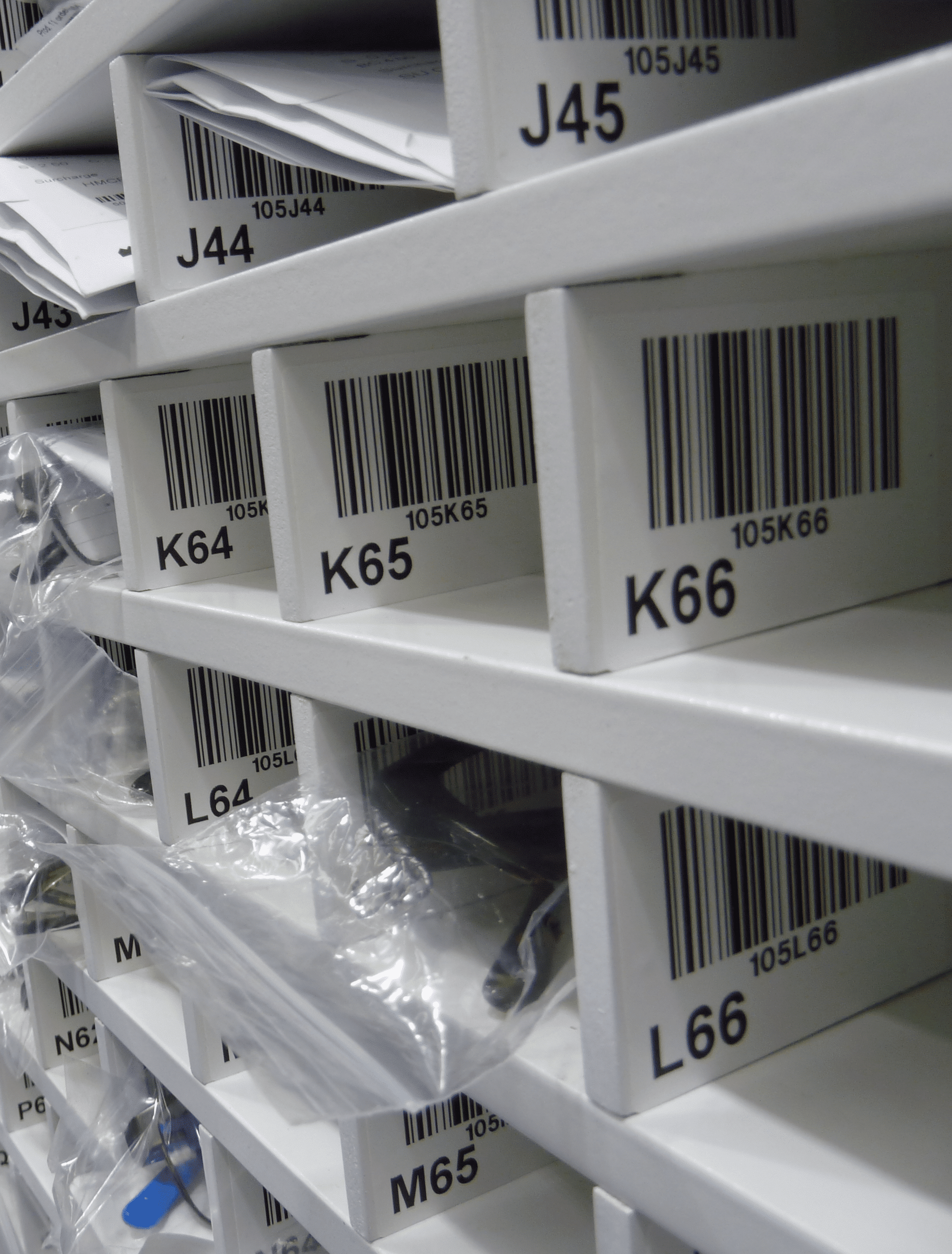
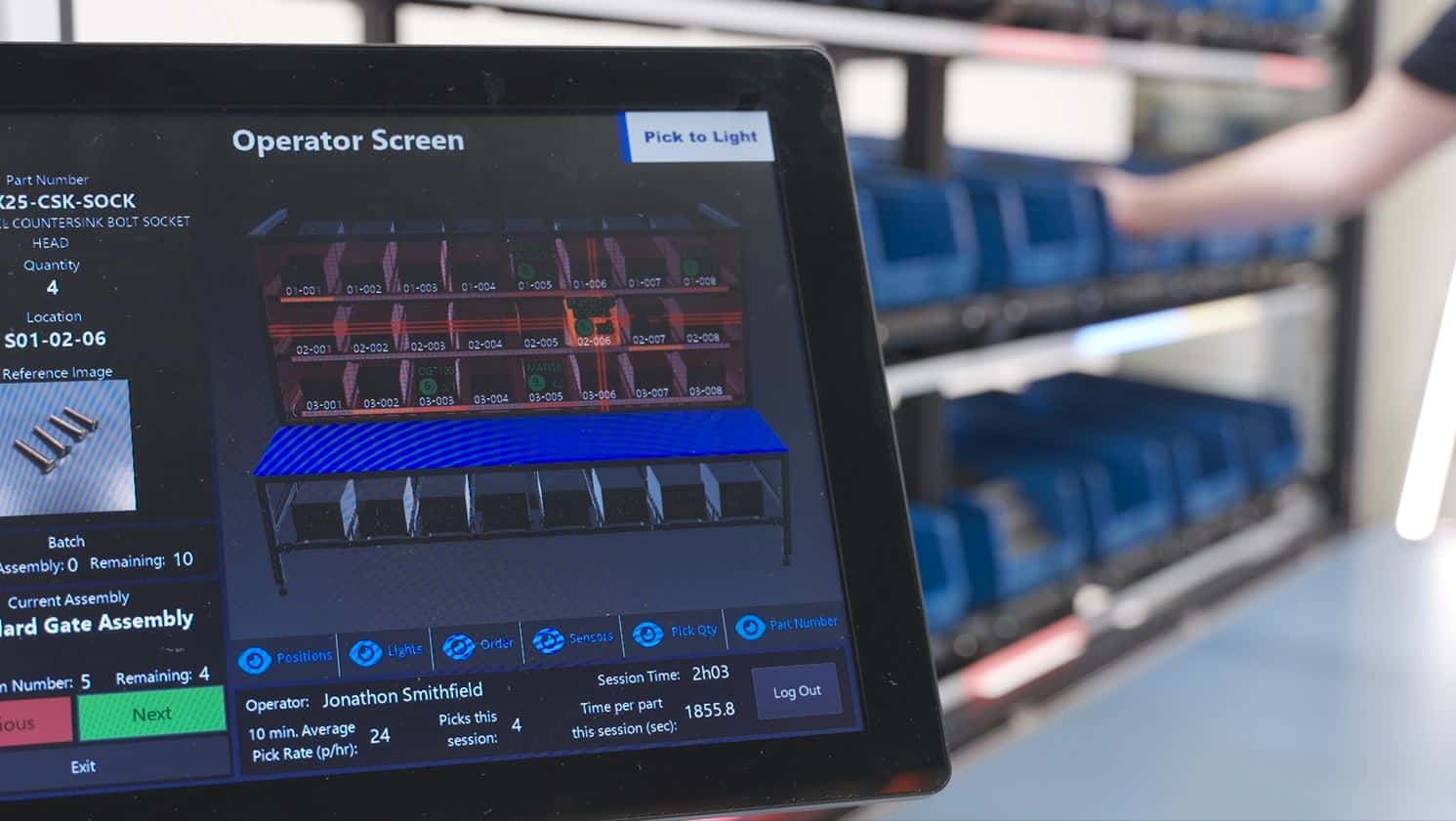
Drawer – Pick to Light System: Suitable for small to medium-sized products in the optical, postal, e-commerce, pharmaceutical, medical kits, tablets, medications, and dispensaries industries. It allows for storing a larger quantity of product in a specific area.
Standard containers or existing shelves can be reused because our Pick to Light system can be installed at the front of existing drawers. The systems can be adapted to the size and shape of the product and the picking process. The system is also easy to expand in modular sections.
Technical Features
Pick to Light and Barcode Software
Our software controls the LED lighting of all locations. The number of locations can range from a few hundred to over twenty thousand. Our addressable lighting system eliminates the need for large amounts of wiring, resulting in a simple and easy-to-maintain design.
Our wireless and Ethernet barcode system allows staff to move freely around the warehouse area and pick products using the latest portable barcode scanners.
Data retrieval is carried out with our OSG Web Call software, which communicates with the customer’s warehouse management system or the factory’s database software. Integration with the customer’s warehouse management system allows for seamless communication and real-time inventory monitoring.
This allows us to retrieve work information, bills of materials, and part numbers to then store them or use them to route and store products.
Our database system records the location of everything within the Pick Face store.
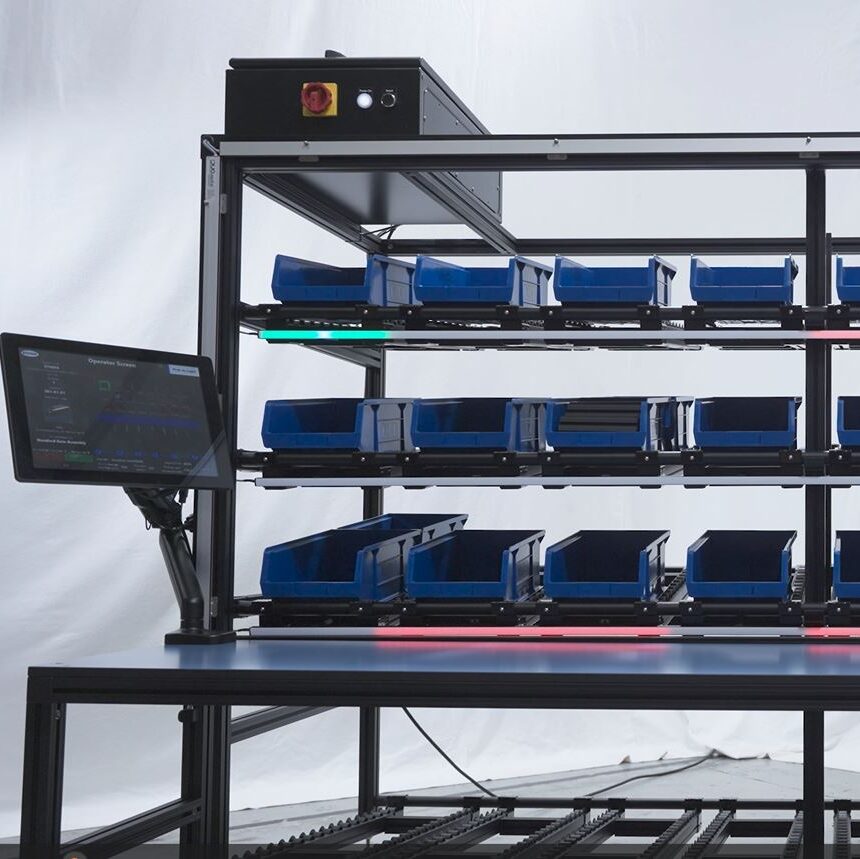
Remote access to both the PC/PLC and the barcode system means we can provide comprehensive support and service.
Contact us for more information about our Pick to Light system.