GoPal E22 Features
The GoPal E22 is designed to transport light to medium-weight loads (up to 500 kg) on standard European pallets or half European pallets. This autonomous mobile robot (AMR) is ideal for optimizing internal material transport in various industries.
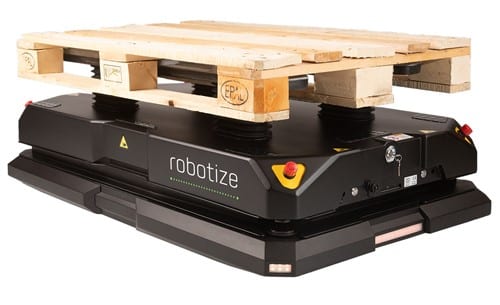
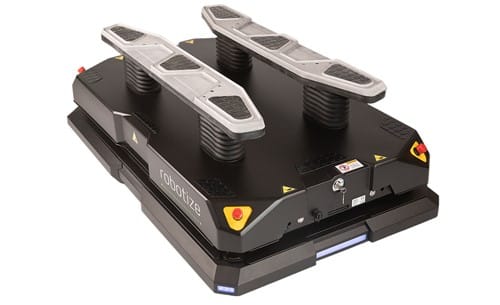
GoPal E22 Specifications
Application: Autonomous mobile robot (AMR) for transporting European pallets/half European pallets with light to medium-weight loads.
Physical dimensions:
- Length x Width x Height: 1400 x 860 x 340 mm
- Mass: 187 kg
Performance:
- Battery life (autonomy): 6-14 hours (or up to 20 km)*
- Maximum speed: 2.4 m/s (8.6 km/h)*
- Turning diameter: On-site rotation (950 mm)
Safety:
- Laser scanners (360° protection)
- Mechanical bumper (360° protection)
- 4 emergency stop buttons
Additional Obstacle Avoidance Sensors:
- 3D cameras (two front and one rear)
Battery:
- Type/Voltage: LiFePO4 / 48V
- Charging time: 45 minutes (full charge)
- Number of charges: Approximately 5,000
Charger Interface:
- Automatic coupling interface (at the front of the robot)
- Connector for manual charging (at the rear of the robot)
Communication:
- Wi-Fi 802.11ac
Environmental Features:
- Operating temperature: -10°C to +45°C
- Humidity (max.): 95% (non-condensing)
Floor Requirements:
- Average slope (max.): Nearly level (2%)
- Friction coefficient (min.): 0.60
- Maximum edge height: 4 mm
Load:
- Maximum load: 500 kg
- Maximum length: 1240 mm
- Maximum width: 820 mm
- Maximum height: 2400 mm*
Pallet types:
- Standard European pallets / Half European pallets. Others upon request.
Pallet Condition:
- Undamaged, with original strength maintained (Grade A or B)
Lane Conditions:
- Minimum lane width: 1200 mm
- Recommended lane width: 2100 mm
- High-speed lane width: 2800 mm *depending on load conditions
Safe and Fully Automated Transport: Safely automates internal material transport while collecting all necessary data to continuously optimize intralogistics.
Supports Different Loads: Compatible with various loads and pallet types.
Data Collection, Analysis, and Reporting: Continuous monitoring and data analysis to improve operational efficiency.
Automated Pickup, Transport, and Delivery: Comprehensive functionality covering the entire pallet handling cycle.
Automatic Battery Charging: Automatic charging during downtime opportunities to maintain operational efficiency.
Agile Performance and Autonomous Navigation: High maneuverability and autonomous navigation for dynamic environments.
Plug-and-Play Flexibility: Easy integration and setup into existing systems.
ERP/WMS Integration: Compatible with enterprise resource planning and warehouse management systems.
Simple and Intuitive Interface: Easy to use for quick adoption and efficient operation.
Available in various sizes for standard European, industrial, and combined pallets, as well as US/UK pallets. The station enables precise pallet placement.
Allows the combination of multiple pallet stations for reduced overall space usage.
Designed for fast, fully automatic charging in just 45 minutes.
Supports European, half, and industrial pallets. Manual, semi-automatic, and fully automatic operation.
Mobile Lifting Station: Enables mobile palletization with easy and secure access to the pallet, continuously adjusting the pallet height.
Conveyor Station (E): Seamless integration with traditional conveyor systems, supporting loads up to 750 kg. <br>Conveyor Station (EW): Supports standard European and industrial pallets with loads up to 1500 kg. <br>Conveyor Station (U): For handling US/UK pallets with loads up to 1500 kg.
Allows manual robot summons to pick up a pallet and transport it to a preprogrammed destination.
Similar to the single button but with five preprogrammed destinations.
Auxiliary interface with six I/Os to connect the GoPal solution to external devices.
Automatically detects the presence or absence of a pallet at the pallet station.
Provides additional visibility of the robot on the factory floor, flashing green when the robot is in motion.
Fleet management system that controls everything in your GoPal solution, including order queues, system component status, and real-time robot tracking.